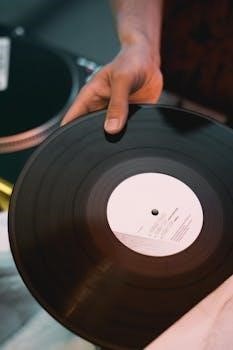
standard o-ring groove dimensions pdf
O-Ring Groove Dimensions Overview
This section provides an overview of O-ring groove dimensions, encompassing width, depth, and tolerances for both static and dynamic applications. It highlights the importance of proper groove design for effective sealing. Standard dimensions are crucial, and the information here will guide users in selecting the correct dimensions.
O-ring groove design is fundamental to achieving reliable sealing in various applications. The groove’s dimensions, including width and depth, directly impact the O-ring’s performance. A properly designed groove ensures the O-ring is compressed sufficiently to create a tight seal without excessive deformation, which could lead to premature failure. Considerations include both static and dynamic applications, each requiring specific groove parameters. The O-ring’s material, size, and the operating environment are all crucial factors in determining the optimal groove dimensions. For example, vacuum applications may require a different approach compared to standard seals. Furthermore, tolerances for the groove dimensions must be carefully considered to ensure consistency and reliability in manufacturing. The design process also includes the need to review standards and manufacturer guidelines, often available in PDF resources. Understanding these principles is the first step towards creating effective and durable sealing solutions. Factors such as surface finish and the potential need for back-up rings may also influence the design of the O-ring groove.
Standard O-Ring Groove Width Dimensions
Standard O-ring groove width dimensions are crucial for ensuring proper seal function. These dimensions are typically determined by the O-ring’s cross-sectional diameter and the intended application, whether static or dynamic. The groove width must be wide enough to accommodate the O-ring, allowing for some compression, but not so wide that it allows excessive movement or extrusion. For static seals, the groove width is usually tighter than for dynamic applications, where slight movement is expected. Standard charts, often found in PDF resources, provide precise measurements for various O-ring sizes. These charts often include nominal groove widths and associated tolerances. It is important to note that groove width can vary based on whether the O-ring is used in an internal or external groove. The proper width ensures that the O-ring remains stable and performs its sealing function efficiently. It’s also essential to consider the use of back-up rings, which may influence the required groove width. These specifications are critical in design and manufacturing to avoid seal failure. Deviation from recommended groove widths could cause leakage or damage to the O-ring. Precise adherence is key for a successful seal.
Standard O-Ring Groove Depth Dimensions
Standard O-ring groove depth dimensions are equally vital to ensure effective sealing. The groove depth must be carefully calculated to provide the correct compression on the O-ring, enabling it to create a tight seal without excessive deformation. Too shallow a groove will not allow sufficient compression, leading to leaks, while a groove that is too deep can result in O-ring extrusion or damage. Standard depth dimensions are usually defined in relation to the O-ring’s cross-sectional diameter. These dimensions vary based on whether the application is static or dynamic. For static seals, the groove depth is generally designed to provide a higher level of compression compared to dynamic seals, where movement must be accommodated. Standard charts and PDF resources provide specific groove depth dimensions for different O-ring sizes and application types. These charts often include tolerances which should be closely followed during manufacturing. The correct depth ensures the O-ring maintains the necessary sealing force and avoids premature failure. Consideration must be given to the operating pressure. The correct groove depth contributes to a reliable and durable seal. Proper depth is crucial in the overall sealing performance of the system.
Tolerances for O-Ring Grooves
Tolerances for O-ring grooves are critical to ensuring the proper function and longevity of the seal. These tolerances specify the acceptable variation in groove dimensions, including width and depth, during the manufacturing process. Adhering to these tolerances is essential to guarantee that the O-ring is compressed correctly, providing an effective seal without excessive stress or premature failure. Standard tolerances for O-ring grooves are usually defined in engineering standards and vary depending on the application and O-ring size. For instance, static seals may have tighter tolerances compared to dynamic seals, where a greater degree of movement is involved. These tolerances are typically expressed as plus or minus deviations from the nominal groove dimensions. Exceeding these tolerances could result in improper seal performance, leading to leaks or seal damage. When designing O-ring grooves, engineers should carefully consider the manufacturing process and select tolerances that are achievable and cost-effective. Referencing standard charts and PDF resources will provide the necessary tolerance information. Proper adherence to specified tolerances is crucial in maintaining the integrity and performance of the O-ring seal and overall system reliability.
O-Ring Groove Dimensions for Static Seals
Static seals, where there is no relative motion between the sealed components, require specific O-ring groove dimensions to ensure effective sealing performance. These dimensions are carefully calculated to provide the correct compression and prevent leakage in static applications. Typically, the groove width for static seals is designed to accommodate the O-ring’s cross-section with a specific squeeze factor, which is the amount of compression applied to the O-ring. The groove depth is also crucial to allow for the proper volume of the O-ring. Standard charts and PDF resources provide these dimensions for various O-ring sizes and applications. Unlike dynamic seals, where movement is involved, static seal groove dimensions are more focused on maintaining a consistent seal under pressure and are typically tighter in tolerance. The dimensions include consideration of the material of the O-ring itself, as well as the material of the components that form the groove. Following these standard dimensions is crucial for achieving reliable static sealing and preventing premature seal failure. Proper design ensures the O-ring is not over or under compressed, which can lead to leaks or reduce its lifespan.
O-Ring Groove Dimensions for Dynamic Seals
Dynamic seals, which involve movement between the sealed components, demand different O-ring groove dimensions compared to static seals. The design must accommodate the O-ring’s movement, preventing excessive friction and wear. Groove width for dynamic seals is generally wider than for static seals, providing more space for the O-ring to move without excessive compression or pinching. The groove depth must allow the O-ring to roll or slide freely, depending on the specific application. Factors like lubrication and surface finish also play a significant role in dynamic seal performance. Standard dimensions for dynamic applications are provided in charts and PDF resources, taking into account the type of movement (reciprocating, rotary, oscillating) and the operating conditions. The dimensions also consider the material properties of both the O-ring and the groove materials. Precise dimensioning prevents premature failure, leakage, and excessive wear. Unlike static applications, where the O-ring is compressed and held in place, dynamic seals require more clearance to accommodate movement and prevent damage; Choosing the correct dimensions is vital for reliable sealing in dynamic applications.
O-Ring Groove Dimensions for Vacuum Applications
O-ring groove dimensions for vacuum applications require special considerations due to the unique demands of low-pressure environments. Unlike standard sealing, vacuum seals must prevent air from entering the system, necessitating precise dimensions and surface finishes. Groove design in vacuum applications typically involves a reduced groove width compared to standard seals to ensure proper compression and sealing under low pressures. Groove depth is also carefully calculated to prevent the O-ring from being squeezed too tightly, which could lead to outgassing. Surface finishes for vacuum grooves need to be very smooth to minimize leakage. The selection of O-ring material is critical to prevent outgassing and maintain sealing properties. Vacuum O-ring dimensions are often specified in technical resources, including PDF documents with detailed diagrams and tables; The dimensions vary depending on the specific application and the level of vacuum required. Vacuum O-rings are designed to withstand these pressures without deformation or leaks. Precise O-ring groove dimensions are crucial to achieve a reliable vacuum seal in various applications. These dimensions are different from standard seals.
O-Ring Groove Dimensions in Boss Seals
Boss seals, often utilized in hydraulic and pneumatic systems, incorporate O-rings to create reliable connections. The O-ring groove dimensions within these boss seals are essential for proper function and leak prevention. The dimensions, including groove width and depth, are generally integrated into standard specifications for boss seal designs. These dimensions are carefully calculated to ensure the O-ring is compressed sufficiently to create a tight seal without being over-compressed, which could cause damage. The precise dimensions of the O-ring groove ensure the seal can operate effectively under pressure; The groove typically has straight sides, offering a stable and consistent sealing surface. Surface finish on the groove is also important to prevent any leakage. The dimensions are usually found in engineering handbooks and PDF documents. These resources provide detailed tables for various boss seal types and sizes. Proper groove dimensions are critical for preventing leaks and maintaining system integrity. The dimensions are often standardized to facilitate easy interchangeability and consistent performance. O-ring grooves in boss seals are designed to perform reliably in demanding applications. The right dimensions ensure a secure connection.
O-Ring Groove Dimensions with Back-up Rings
When O-rings are used in high-pressure applications, back-up rings are often incorporated to prevent extrusion and enhance seal performance. The inclusion of back-up rings influences the O-ring groove dimensions. The groove needs to accommodate both the O-ring and the back-up ring(s) properly. Typically, one or two back-up rings are employed, depending on the pressure requirements. The groove width must be increased to accommodate the added thickness of the back-up ring(s). The groove depth might also be altered to ensure the correct compression of the O-ring without over-compressing the back-up rings. The dimensions for these grooves are often provided in engineering handbooks and PDF resources. The dimensions also depend on the type and size of the back-up ring used, spiral wound or solid. The groove must also provide adequate space to prevent the back-up rings from binding or causing issues during assembly. Proper design of the groove with back-up rings ensures the seal can withstand higher pressures. Utilizing the correct dimensions is essential for reliable sealing and prevention of leaks; These dimensions are critical for maintaining system integrity and optimal performance. Back-up rings are crucial for extending the life of the O-ring, and proper groove dimensions are essential for the back-up rings to function correctly.
O-Ring Groove Surface Finish Considerations
The surface finish of an O-ring groove is a critical factor that significantly impacts seal performance and longevity. A rough surface can create pathways for leakage, while an overly smooth surface might hinder proper O-ring compression. The ideal surface finish is one that provides a balance between these two extremes. For static applications, a smoother finish is generally preferred to prevent leakage. For dynamic applications where the O-ring moves, a slightly rougher finish can aid in lubrication and reduce friction, but care must be taken to avoid excessive roughness that could damage the seal. The surface finish is typically measured in micro-inches or micrometers, and specific values are often recommended in engineering standards and O-ring manufacturer guidelines. Proper surface finish ensures the O-ring has proper contact with the groove and provides a reliable seal. The surface finish is a factor that should not be overlooked. The surface finish must be carefully controlled during machining to ensure the groove is within the required tolerance. The proper surface finish helps prevent leaks, and aids in O-ring durability. Surface finish specifications are often included in PDF resources regarding O-ring groove design and dimensions. These values should be strictly adhered to during manufacturing.
PDF Resources for O-Ring Groove Dimensions
Numerous PDF resources are available offering detailed specifications and guidelines for O-ring groove dimensions. These resources typically include comprehensive charts and tables that outline standard groove widths, depths, and tolerances for various O-ring sizes. These PDFs often cover static and dynamic seal applications, as well as specialized cases such as vacuum sealing and boss seals. Many documents provide cross-sectional diagrams that illustrate the proper geometry of the O-ring and groove interface. Furthermore, some PDF documents include information on the recommended surface finishes for grooves. These resources are invaluable for design engineers and machinists as they provide a standardized reference for proper groove design. They facilitate accurate part creation and reduce the likelihood of seal failures. The PDFs are often published by O-ring manufacturers and industry organizations. These PDF resources sometimes include material compatibility charts and installation guidelines. These resources are usually in a downloadable format, allowing for easy access to the information. They also aid in the selection of the appropriate O-ring and groove dimensions. These documents are invaluable for anyone working with O-rings, ensuring correct application.